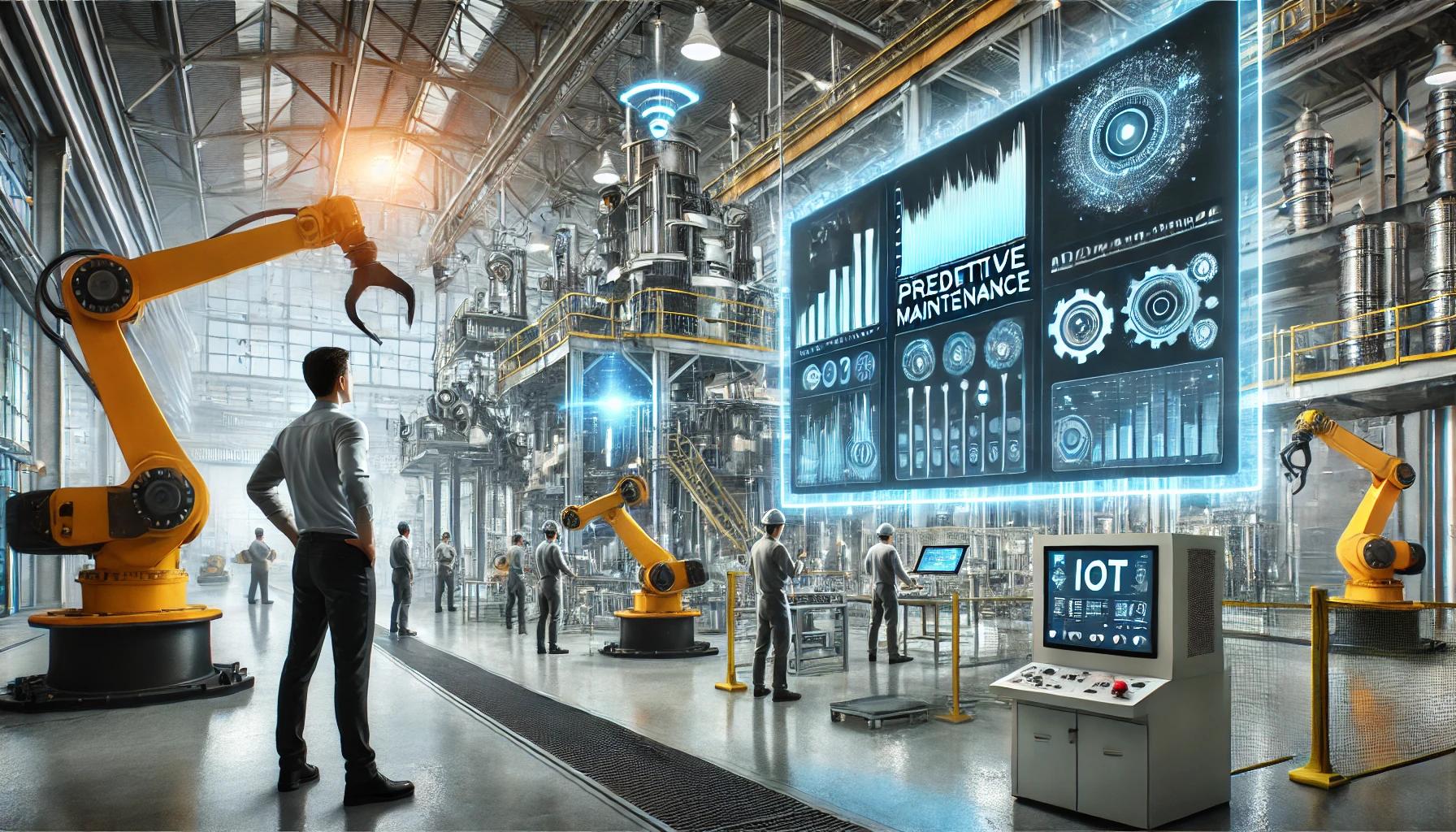
Predictive Maintenance in Industry 4.0: How Connectivity is Transforming Machine Reliability
Predictive Maintenance in Industry 4.0: How Connectivity is Transforming Machine Reliability
Introduction
The rise of Industry 4.0 has brought significant advancements in machine connectivity and data-driven decision-making. One of the most impactful applications is predictive maintenance, which leverages IoT sensors, artificial intelligence (AI), and real-time analytics to anticipate and prevent equipment failures before they occur.
Traditional maintenance methods, such as reactive (fixing after failure) and preventive (scheduled maintenance), often lead to downtime, inefficiencies, and unnecessary costs. Predictive maintenance offers a smarter approach, ensuring higher reliability, reduced costs, and optimal machine utilization.
What is Predictive Maintenance?
Predictive maintenance (PdM) uses real-time machine data, IoT connectivity, and AI-driven insights to predict potential equipment failures before they happen. This helps manufacturers:
✔ Reduce downtime by scheduling maintenance only when needed.
✔ Extend equipment lifespan by avoiding unnecessary wear and tear.
✔ Optimize operational costs by reducing emergency repairs and maintenance costs.
✔ Enhance safety by preventing unexpected machine failures.
By integrating sensors, cloud computing, and AI algorithms, predictive maintenance transforms how industries maintain and manage machinery.
How Does Predictive Maintenance Work?
Predictive maintenance relies on a combination of connected devices, machine learning, and data analytics to assess equipment health. The process involves:
1️⃣ Data Collection – IoT sensors continuously monitor machine parameters like temperature, vibration, pressure, and motor efficiency.
2️⃣ Data Transmission – Real-time data is sent to cloud-based platforms for processing and analysis.
3️⃣ AI-Based Analysis – Machine learning algorithms analyze data patterns to detect early warning signs of failure.
4️⃣ Predictive Alerts – The system provides alerts and maintenance recommendations to technicians.
5️⃣ Action & Optimization – Maintenance is scheduled at the most cost-effective and least disruptive time.
💡 DigiSense Smart Maintenance Solutions provide real-time predictive insights, allowing manufacturers to take proactive actions.
Benefits of Predictive Maintenance in Industry 4.0
1. Increased Machine Uptime
Predictive analytics reduces unexpected breakdowns, ensuring smooth production processes.
2. Lower Maintenance Costs
By servicing machines only when needed, manufacturers avoid unnecessary labor and part replacement costs.
3. Extended Equipment Life
Detecting early warning signs prevents major failures, increasing the lifespan of industrial assets.
4. Improved Worker Safety
Preemptively addressing equipment malfunctions reduces accidents and hazardous situations.
5. Real-Time Decision Making
With IoT and AI, businesses can make data-driven maintenance decisions, optimizing workflows.
📢 Case Study: A manufacturer reduced unplanned downtime by 40% after implementing a predictive maintenance strategy powered by AI-driven sensors.
Predictive Maintenance vs. Preventive Maintenance
Maintenance Type | Description | Key Advantage |
---|---|---|
Reactive Maintenance | Fixing after failure | Low initial cost but high downtime risk |
Preventive Maintenance | Scheduled maintenance at fixed intervals | Reduces failures but may lead to unnecessary servicing |
Predictive Maintenance | AI-driven analysis predicts failures before they occur | Optimized maintenance with minimal downtime and cost savings |
Predictive maintenance outperforms preventive methods by enabling just-in-time servicing, ensuring maximum efficiency.
Technologies Powering Predictive Maintenance
🚀 Industrial IoT (IIoT) – Sensors provide real-time condition monitoring of machines.
📊 AI & Machine Learning – AI-driven analytics predict potential failures before they happen.
🌐 Cloud Computing – Stores and processes vast amounts of machine data for predictive insights.
📡 5G Connectivity – Enables high-speed data transfer for instant machine monitoring.
🔧 Digital Twins – Virtual replicas of physical machines help simulate and analyze performance.
💡 DigiSense Smart Maintenance Suite integrates these technologies for seamless predictive maintenance implementation.
Challenges in Implementing Predictive Maintenance
🔴 High Initial Investment – Requires IoT sensors, AI tools, and infrastructure upgrades.
🔴 Data Complexity – Large volumes of machine data require powerful analytics solutions.
🔴 Workforce Training – Operators and technicians need training to use advanced maintenance tools.
However, with DigiSense AI-driven solutions, manufacturers can overcome these challenges through scalable, cost-effective predictive maintenance strategies.
Key Performance Metrics for Predictive Maintenance
Tracking the right KPIs ensures successful predictive maintenance implementation:
Metric | Definition |
---|---|
Mean Time Between Failures (MTBF) | Average time a machine operates before failure |
Mean Time to Repair (MTTR) | Time taken to restore a machine after failure |
Downtime Reduction % | Percentage of unplanned downtime reduction |
Maintenance Cost Savings | Total cost reduction due to optimized maintenance |
Analyzing these KPIs helps refine maintenance strategies for maximum efficiency.
Conclusion
Predictive maintenance is a game-changer in Industry 4.0, leveraging IoT, AI, and real-time analytics to prevent failures, optimize efficiency, and reduce costs.
At DigiSense, we help manufacturers:
✔ Deploy AI-driven predictive maintenance solutions
✔ Monitor machine health in real time
✔ Reduce downtime and lower maintenance costs
📢 Ready to optimize your industrial maintenance? Contact DigiSense today for a tailored predictive maintenance strategy! 🚀